In this informative article, we will explore the key points of formula design for PVC compound for cable.
Magnesium hydroxide is a versatile substance with various applications, including water treatment, building materials, and the cable industry. At Green PVC, we have devoted extensive efforts to harnessing magnesium hydroxide as a flame retardant specifically for cables. We offer Brucite (a mineral form of magnesium hydroxide) B3.5SA for PVC compound. Our range includes precipitated magnesium hydroxide PM5SN for halogen-free flame retardant cable compound. We recently developed a new grade called PM3SL for the HFFR compound. This innovative solution performs excellently and comes at a lower cost compared with PM5SN.

During our extensive promotion and testing of magnesium hydroxide, we were flooded with questions from our PVC compound manufacturing customers. And what were they most curious about? The formula of PVC compound. Today, we’re excited to share some crucial insights into the formula design PVC compound for cable. Get ready for a deep dive into the world of PVC formulas that will leave you feeling inspired and knowledgeable. Let’s get started and enjoy the journey!
What’s Inside? Uncover the Ingredients of Our PVC Compound for cable
Ready to dive into the inner workings of formula design? First, let’s demystify the materials behind the PVC compound formula. We create the magic by using polyvinyl chloride as the foundational resin and incorporating stabilizers, lubricants, and inorganic fillers. The PVC compound for cable comes to life through a careful mixing, kneading, and extrusion process.
Now, let’s focus on the crucial elements of PVC formula design. Join us as we explore the selection of PVC resin, stabilizers, lubricants, and inorganic fillers—the building blocks for crafting exceptional PVC compounds for cable formulas.
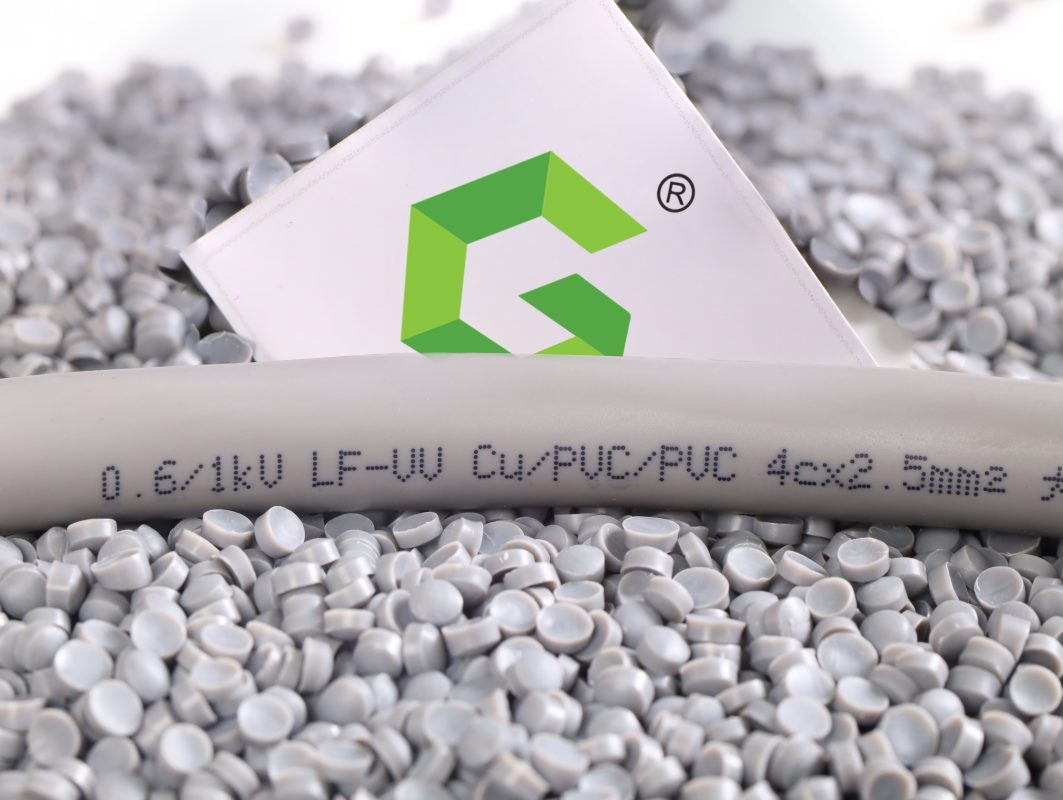
PVC compound for cable formula: A guide you won’t want to miss
Discover the essential aspects of PVC compound for cable formula design.
1. For general sheath grade PVC compound for cable, the recommended amounts are as follows: plasticizer (0-60PHR), stabilizer (6-8PHR), lubricant (1.5-2PHR), and filler (10-20PHR).
✅Increase the plasticizer amount if it has poor plasticizing efficiency.
✅When using a large amount of filler, increase the amounts of plasticizer and lubricant accordingly.
✅When using inactive fillers, increase the amounts of plasticizer and lubricant. Adding a 5PHR cold-resistant plasticizer is advised for sheath-level cable compound.
2. For general insulation cable compound, the recommended amounts are as follows: plasticizer (40-50PHR), stabilizer (6-8PHR), lubricant (1-1.5PHR), and filler (10PHR).
3. Avoid using cable materials with DBP that have high volatility.
4. For a high-temperature resistance cable compound, use a high-temperature resistance plasticizer and increase the amount of plasticizer. Add 0.3-0.5PHR antioxidant.
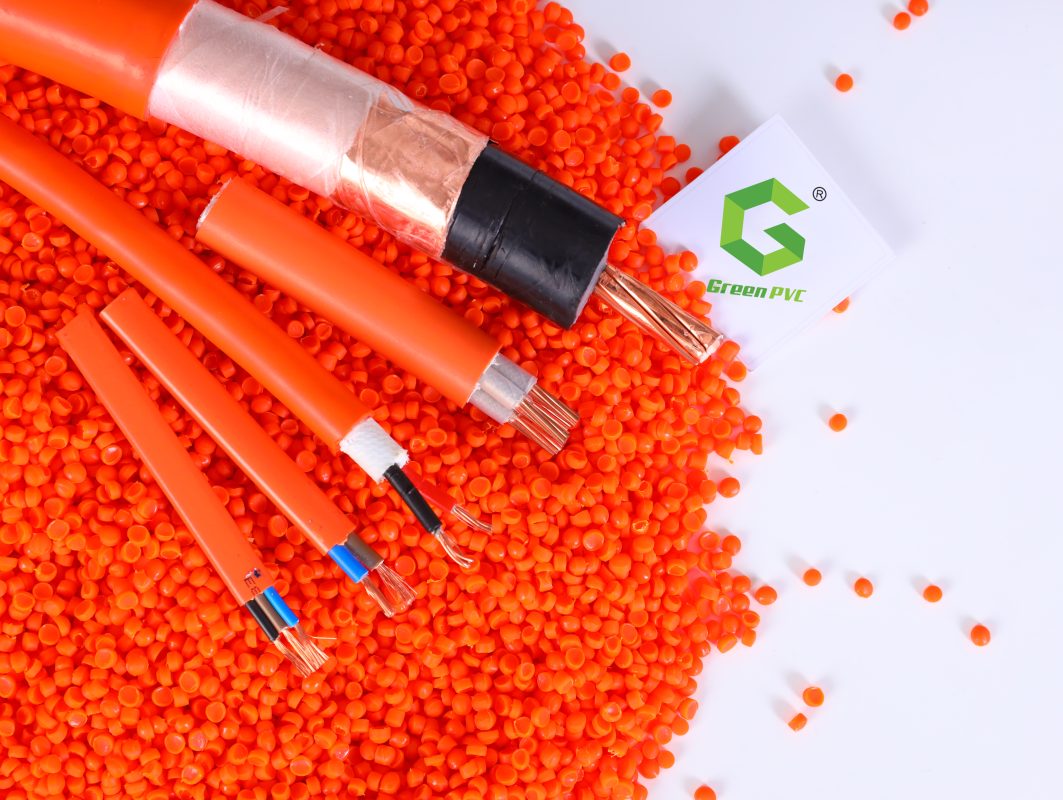
5. Use fillers like calcined clay for cable materials requiring high insulation performance. Note that high polymer plasticizers have lower plasticization efficiency, so adjust the amount of plasticizers accordingly during formulation.
6. To create a transparent compound, it is important to use plasticizers compatible with the resin. Transparent stabilizers like organotin are recommended, but the amount of lubricant added must be strictly controlled.
7. Choosing a composite flame-retardant system is advisable When designing a formula for flame-retardant cable material.
8. Compound processing modifiers can be used to formulate a high polymerization degree cable compound to improve its processing performance.
9. polyester or high molecular polymer plasticizers should be chosen when formulating a non-migrating compound.
10. When selecting a compound stabilizer, slightly more dosage should be used compared to stabilizers like tribasic.
11. When the cable material is being processed and used normally, it is important to minimize the amount of stabilizer to avoid excessive use and the “filler effect.”
At Green PVC, we prioritize these standards and offer top-notch PVC compounds that meet all requirements. Join us on an innovative journey and get the latest offers by messaging us today. We value your feedback, so please get in touch with us with any suggestions. That wraps up today’s update.
Discover more about our products
Differences between flexible and rigid PVC compounds
Why Green PVC’s Flexible PVC Compounds Are the Choice for Industry Leaders
The Comprehensive Guide to Rigid PVC Compounds from Green PVC
Crystal Clear Solutions with Transparent PVC Compounds from Green PVC
Nhat Huy Group is a leading Vietnamese manufacturer and exporter of various products. Founded over a decade ago, we have been doing business with customers worldwide, spreading across five continents. Green PVC JSC is a PVC compound factory belonging to Nhat Huy Group. Since its inception, the Board of Directors has oriented the company toward industrial production. Our factory has modern equipment, machines, and advanced production lines worldwide. |